Warehouse robots and robotics describe the machinery and automation used to improve the efficiency of a warehouse, distribution centre, production facility or another site with a steady flow of goods or materials travelling through it. Call it warehouse robotics or automation machinery; the outcome is the same - streamlining warehouse operations across the board.
Recently, warehouse automation has gained prominence within facility and supply chain management, becoming a significant player in the move towards greater efficiency and capturing a significant advantage over competitors. However, automated warehouse robotics (such as with an automated forklift) is still a relatively new concept.
Many business owners, supply chain professionals and integrated logistics solutions managers will work with more traditional, human-led internal processes. They could be unaware of what this technology is or what is available. This blog explores these concepts and explains where these technologies are commonly adopted and for what purpose.
What types of automation machinery are there?
The landscape of businesses and industry as a whole is increasingly competitive. With large corporations offering services such as next-day delivery, the pressure is on for both manufacturing and distribution to be as quick and as accurate as possible. This is where automated machinery comes in.
Whether the business case involves logistics or manufacturing, automation provides a new dimension of productivity, greater visibility and clarity regarding where products and materials are within the pipeline. This can be done for singular processes such as put-away or replenishment or across an entire logistics infrastructure in a complete system conversion. To understand more about what warehouse automation is, head to our blog post.
There are multiple types of warehouse robotics or automation available today. These include:
Automated Guided Vehicles (AGVs).
AGVs are quickly becoming a popular choice for the transportation of materials within warehouses, replacing the need for human operators to dedicate time to these repetitive tasks and tracking where materials are within a warehouse.
Many work by utilising in-built sensors to detect where they are, map paths and remain safe while operating on the warehouse floor. These machines can be used to automate a vast range of processes, such as block-stacking, light-item handling and high-level storage.
Some fantastic examples of AGVs are automated warehouse trucks and automated tow trains for the transportation of assets such as pallets and cages.
Goods-to-person (G2P) automation.
G2P solutions leverage automated storage systems to transport goods to pick stations, allowing human operators to quickly and accurately fulfil requested orders. The human operator doesn’t have to move around searching for items, as a conveyance method will take over that job and software will track which material or item is needed at the pick station.
Naturally, while G2P represents a significant increase in accuracy when it comes to order fulfilment, they necessitate a potentially demanding change in infrastructure and site build.
Automated Storage and Retrieval Systems (AS/RS).
AS/RS is a system that manages, stores and retrieves goods on demand. Directly controlled through software, systems like these emphasise the fast movement of materials or goods and can typically be found paired with warehouse execution software.
AS/RS uses shuttles or cranes to move around storage aisles and varying heights to move, deposit, and retrieve targeted items when implemented. Again, systems like these help to increase the speed and efficiency of both automated material handling solutions and fulfilment.
Collaborative robots.
In many warehouse environments, employees are required to perform diverse and sometimes complex tasks. Collaborative robots (also known as ‘cobots’) have been designed to assist with these tasks.
Created to be semi-autonomous, collaborative robots can often be found following human pickers through a warehouse, acting as moving storage for pickets goods and materials. Other examples will transport loads or work to direct workflows.
Articulated robot arms.
Articulated robot arms are used for tasks such as packing, palletising and receiving. They utilise multi-jointed limbs to move products efficiently and safely within a distribution centre or warehouse.
Because of their multiple joints, they can nimbly manoeuvre items, parcels and packages into their desired locations without the need for human interaction.
Improve your businesses efficiency with warehouse automation
Download the guide to find out more about warehouse automation. You will also receive guidance on implementing the solution into your operation.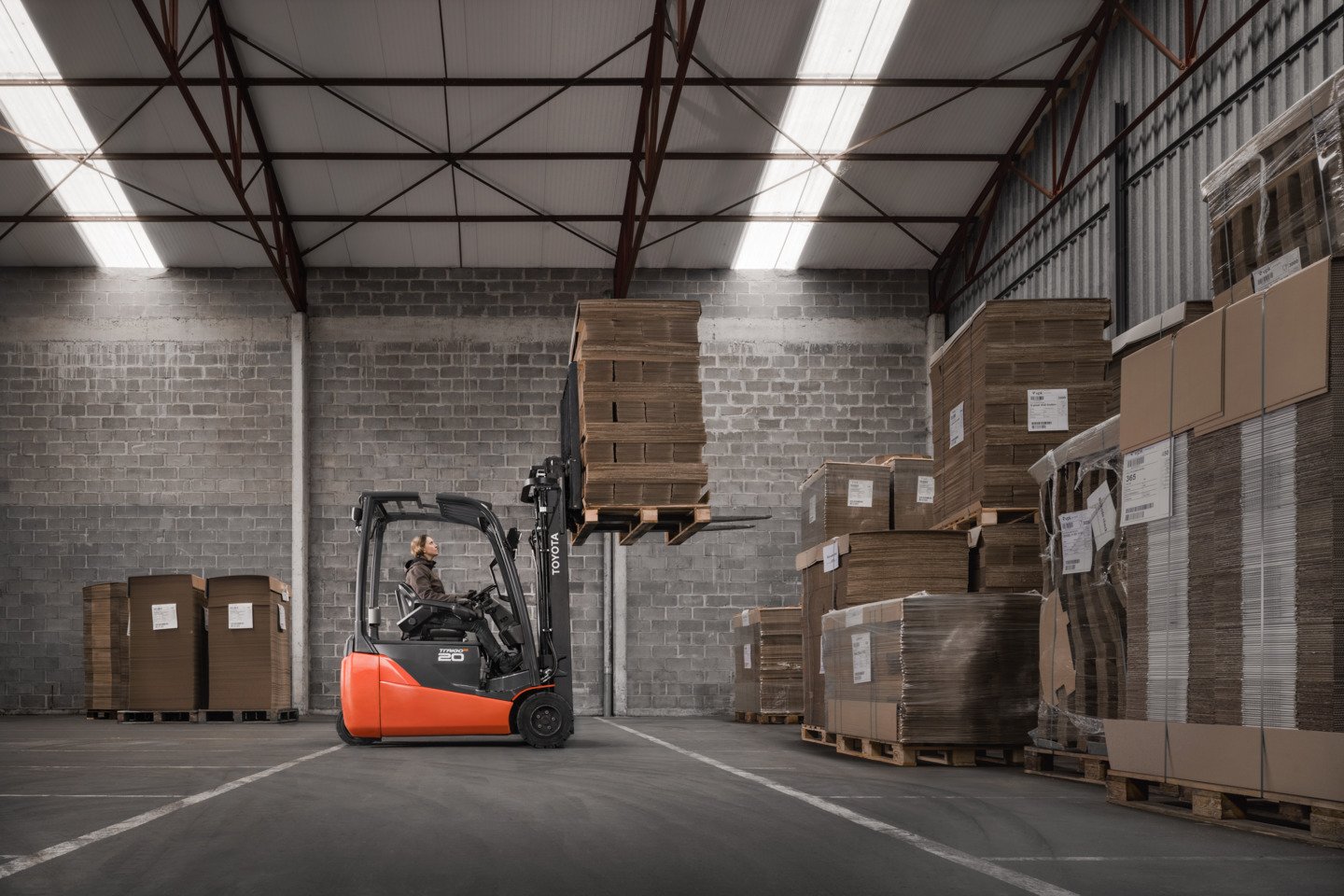
Use cases for warehouse robots.
There are many uses for robotics and automation within a warehouse setting. They play a critical role in enabling the flow of goods and raw materials from their starting point to their intended destination - all while maintaining safety standards and accuracy.
They aid in the fulfilment process, help to balance the need for human labour and deal with the rising costs of employment. So what are the specific use cases for warehouse robotics? These types of machines can be used in:
- Replenishment: Through automating and tracking replenishments, raw materials can remain at healthy levels without the need for last-minute re-ordering.
- Picking: Robots designed to support the picking process help to reduce processing times.
- Transportation: Solutions such as conveyors or AGVs reduce the need for repetitive transportation tasks and ensure employees can focus on bigger-picture tasks.
- Sorting: These machines can be integrated with AI to manage sorting and even sort batch-picked items into sort walls.
- Packaging: In many scenarios, these robots will determine the packaging needed for specific items after analysing weight and dimensions.
Overall, robotics and warehouse automation in the form of solutions such as automated tow trains or shuttles work to deliver significant increases in speed, agility, accuracy and visibility, ensuring stakeholders have a good view of stock movement and manufacturing/fulfilment workflows.
They also greatly reduce human error, delays and can even secure cost-saving benefits for an organisation. So, with the knowledge of these benefits and the types of warehouse automation available today, it’s time to ask the question - is warehouse automation right for you?
Is warehouse automation the right choice for you?
While warehouse automation is becoming increasingly common (as an alternative to forklift rental solutions) and the benefits are undeniable, it is not always the right choice for a business. The specific requirements these machines and automation systems meet are unique, so it is wise to investigate just what position your organisation is in before choosing to utilise equipment such as warehouse robotics.
To aid in your decision-making process, our warehouse automation blueprint will pinpoint the exact questions you should ask yourself to determine whether automation is the right choice for you. From questions regarding labour, warehouse efficiency and delays to considerations regarding automation providers, this is the place to begin. Access the resource below.