From space optimisation to system automation and the use of Automated Guided Vehicles (AGVs), improving warehouse processes is a key consideration for warehouse management and logistics teams. Not only do improvements like these increase safety, manufacturing efficiency or distribution accuracy, but they can also ensure cost-savings and increase customer satisfaction. These are all desirable benefits any company can use to their distinct advantage.
It all starts in the warehouse, where continuous improvement can be seen first-hand and defects can be dealt with. So how exactly can businesses improve their warehouse processes? Here are five key ideas to consider.
- Optimise warehouse space.
- Adopt a warehouse management system (WMS).
- Ensure lean inventory and manufacturing.
- Collect employee feedback.
- Automate your warehouse processes.
1. Optimise warehouse space.
Within a warehouse or distribution centre, space is a vital commodity. A lack of space or the inefficient use of space is a true obstacle to warehouse process improvement.
Businesses and warehouse management teams can make use of vertical height for storing materials, goods or equipment. Taller storage units are useful, especially when paired with the right automated equipment that can be utilised to effectively store, locate, transport or replenish goods and materials in these storage racks. Taller storage areas ensure better use of square footage, getting more out of the same amount of space.
You can even adopt automation solutions such as Radioshuttles. These are high-density storage solutions that can use up to 80% of warehouse volume, increasing overall storage space and throughput. You can find out more about these solutions here.
Logistics and warehouse management should also consider the type of storage shelves they use. Large, deep shelves make no sense for smaller items that can be easy to misplace. Various racking solutions should be placed in designated areas to accurately sort goods and materials.
Finally, remember to regularly review your picking routes, which could not be as efficient as first thought upon further inspection. Test alternative routes to find out whether there is anything better. This can be done alongside an annual layout review.
Implement warehouse automation and see the results.
If you are considering warehouse automation as a solution, be sure to download our checklist. It explains the benefits of warehouse automation and outlines implementation best practices.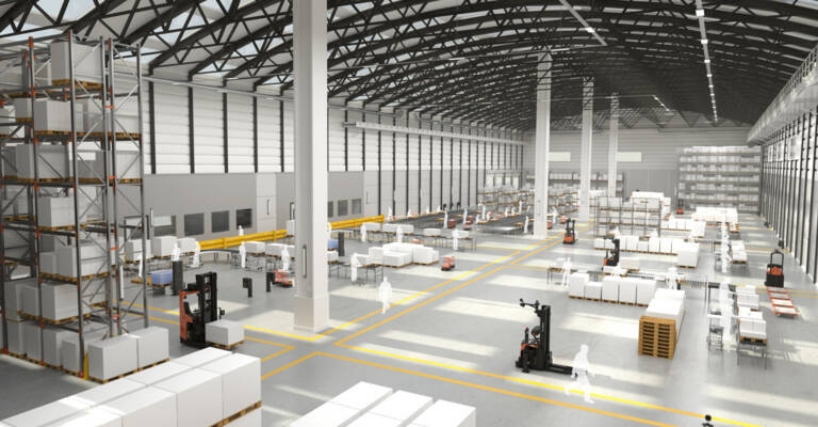
2. Adopt a warehouse management system (WMS).
Efficiency is not found in out-of-date management processes. For example, keeping track of goods or defining transportation routes will not be done in the best way possible through pen and paper. Businesses have a wealth of software and technology at their fingertips to improve efficiency.
Warehouses should adopt a WMS, which increases the visibility of both workflows and the flow of goods through a warehouse, making it easier to spot where inefficiencies occur. A WMS can also create automated pick lists to reduce the potential for mistakes during picking or transactions.
With a WMS, a business can create more accurate orders that arrive on time. This is a distinct advantage for a company, as it was found businesses with perfect order rates of 80 per cent or higher are three times more profitable than those with perfect order rates of 60 per cent. Evidently, this is a popular metric and has a tangible impact on business success.
3. Ensure lean inventory and manufacturing.
Lean inventory is something every warehouse and business, in general, should work towards. The concept of lean inventory and manufacturing originates in early Japanese industrialisation, particularly the automotive industry, where waste is minimised - something we at Toyota Material Handling work towards in our ‘Zero Muda’ (waste) ethos. You can read more about this here.
Lean inventory management and lean manufacturing revolve around optimised utilisation and raw material handling where only what is needed is what is used. There is no waste, no overproduction and no over-ordering. Similarly, truly effective lean inventory or manufacturing will eliminate the need for safety stocks and ensure more accurate deliveries are made, both in and out of a manufacturing or distribution centre.
It is a vital part of what is known as ‘lean infrastructure’, where maximum efficiency is gained through the optimisation of manufacturing, ordering, labour, waste management, fulfilment and other key processes.
4. Collect employee feedback.
One of the best places to gain data regarding warehouse floor processes is from those that carry them out daily. Warehouse employees are the first ones to spot and experience problems and are best-suited to offer solutions that work for them.
Warehouse management should offer a feedback mechanism to collect the knowledge and insights of those directly involved with the day-to-day functions of the warehouse. Sometimes, regular conversations are all that is needed but it can also be done in more formal, trackable means, such as online portals for feedback submissions.
5. Automate your warehouse processes.
Warehouse automation is one of the latest improvements that businesses are becoming aware of. It is a solution that creates a new dimension of productivity within internal processes and is secured by the automation of various everyday processes, such as load handling, replenishment or put-away.
One of the first things to consider when improving warehouse processes is human error. According to a study by Stitch Labs, human error made up 62 per cent of all inventory fulfilment issues. With automation, the chance for these errors to occur is greatly reduced.
In our own words, “No matter the size or type of your business, automation can be an added value.” For example, consider repetitive load handling. That represents a vast amount of time, effort and labour costs, which could easily be automated. From lean transportation to high-level storage, automation grows beyond a warehouse solution, becoming a critical business differentiator.
Automation can be implemented in a step-by-step approach, focusing on specific processes or using a complete conversion to an automated warehouse system. So what are the benefits?
- Automation optimises the flow of goods and minimises damage or risk.
- Employees regain time and can focus on more complex tasks.
- Automated pallet handling requires less energy and maintenance.
- Automation achieves better productivity and a return on investment within two years.
To find out more about warehouse automation, visit our blog here.
If you’re at the point of considering warehouse automation but are still unsure if it will be the right solution for you, use our warehouse automation blueprint to find the answer.
The warehouse automation blueprint.
Inside our warehouse automation blueprint, you can discover the key considerations for a business looking into automation. While there are many ways to improve warehouse efficiency, it’s worthwhile asking the right questions to determine whether automation is the right choice for you.
We cover questions about labour requirements, efficiency demands, warehouse sustainability ideas, common obstacles and information on automation providers. It’s the best place to start for logistics and warehouse management teams considering automation to enhance their warehouse processes.
To access the blueprint, click the link below.