The percentage of businesses reporting “severe to very severe problems” recruiting warehouse staff increased from 0 to 13 percent between September 2020 and September 2021. This shortage makes it challenging for businesses like yours to adapt to seasonal demands and the adverse effect this has on fluctuating labour requirements.
This article will outline four key strategies to help you overcome these challenges and ultimately improve your warehouse labour management. The strategies include:
- Adopt a warehouse management system (WMS).
- Embrace the power of automation.
- Implement a staff training strategy.
- Introduce a fulfilment forecast.
Adopt a warehouse management system (WMS).
Data is one of your most valuable assets when it comes to improving warehouse labour management. This is because it gives you a clear picture of your workflow and the flow of goods coming through your warehouse. By taking the time to analyse your data, you can identify inefficiencies much quicker and devise initiatives to ensure they do not occur in the future.
You can also follow trends and start to predict when certain times of the year will be busy (or less busy) than others. This is extremely valuable for forecasting and deciding what labour requirements you need to meet fluctuating demand.
Adopting a warehouse management system (WMS) is one of the most effective ways to improve your businesses data management. This is because they can provide you with all the data you need in one easy to use place. A WMS can also focus labour on the highest impact activities while finding the most well-suited labourer to perform a specific task. Using labour forecasting, the system can assign jobs on a day-to-day basis and efficiently design schedules.
This is a great way to improve labour, equipment and space efficiency as each of these will be optimised by assigning tasks to the most appropriate people in your workforce.
Embrace the power of automation.
Warehouse automation is another way to overcome the challenges related to fluctuating demand and other elements of warehouse labour management. That is because it offers a solution that creates a new dimension of productivity within internal processes secured by the automation of many everyday tasks.
Some of these include load handling, retrieving stock, replenishment and other types of general labour. A range of Automated Guided Vehicles (AGVs) can remove much of the pressures related to seasonal demand, such as automated warehouse trucks, tow trains, and shuttles.
These types of vehicles are great because they offer your business peace of mind, knowing you have the right technology in place to deal with demand, whether you have too many staff or too little.
Improve productivity and happiness across your workforce.
Discover how to manage staffing issues, adapt to seasonal demand and build a happy, productive workforce by downloading the guide.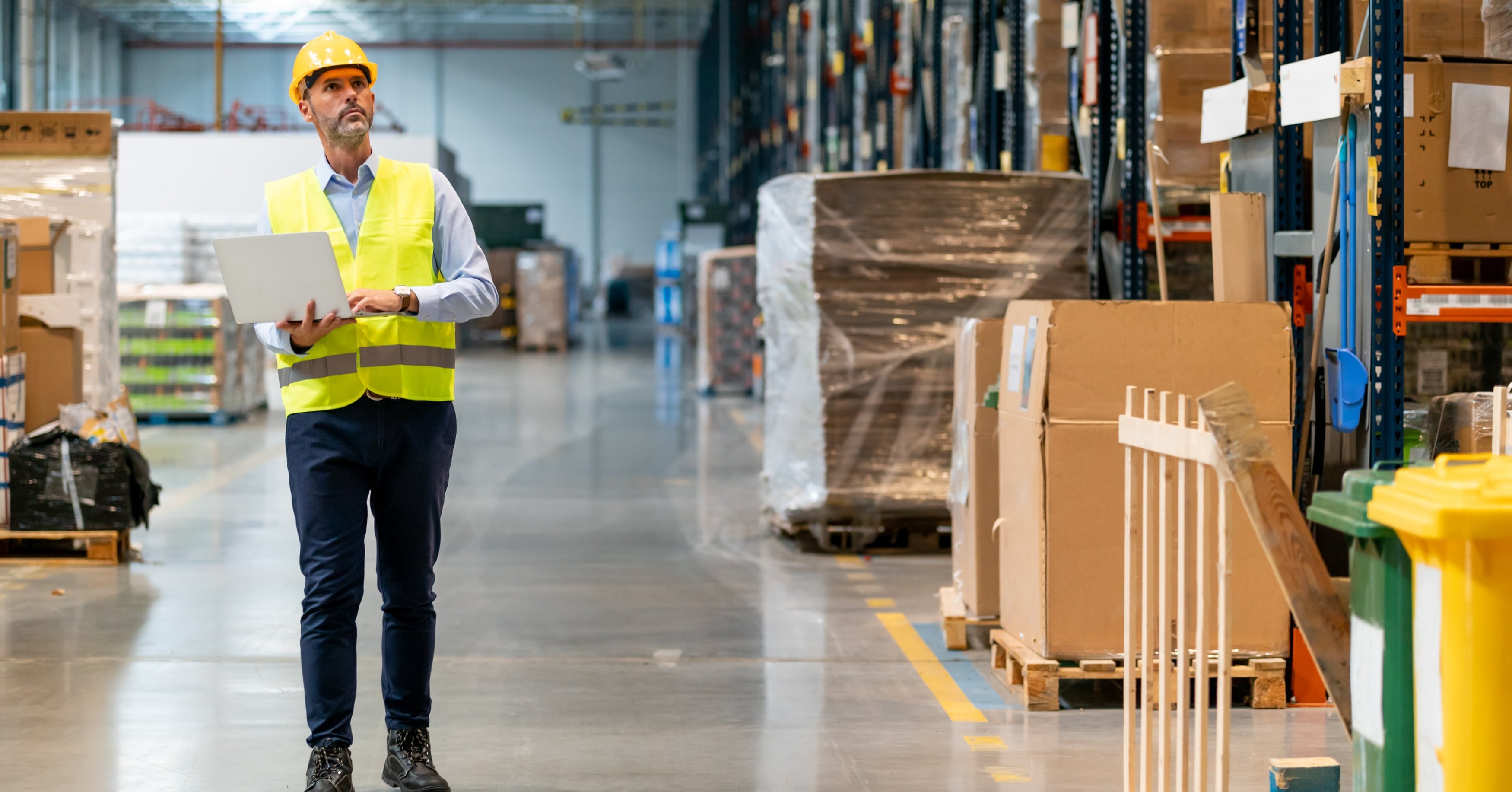
Implement a staff training strategy.
Many businesses fall short when it comes to labour management due to a lack of training investment. This is a crucial step in preparing your workforce to perform tasks to the best of their ability. As new technologies are implemented, the demands of the workforce will also begin to move away from physically demanding tasks to more skilled technical tasks.
Therefore, operators need to upgrade their workers’ skills if they are to remain competitive. This will require investment in reskilling which can only be achieved through effective training. Training your staff will better prepare them for fluctuating demand and also create a culture of safety.
You can find out more about the benefits of operator training here.
Introduce a fulfilment forecast.
Having the ability to create forecasts for your fulfilment team is one of the key benefits of adopting a warehouse management system (WMS).
A fulfilment forecast provides a more accurate view of your consumers' fulfilment choices. This enables businesses to better accurately predict the right amount of inventory required to meet changes in demand. This is a considerable benefit when it comes to improving your warehouse labour management. If your fulfilment team knows when you are more likely to be busy, you can have more staff on board.
However, if the predictions tell your team that a quieter period is coming up, you can reduce the number of workers and decrease your labour costs. There’s a range of qualitative data you can pass on to your fulfilment team to help them better manage workforce requirements depending on seasonal demand. These include:
- Monthly sales averages.
- Historic seasonal sales trends.
- Day of the week sales trends.
- Your previous year’s sales figures.
These are just a few of the strategies available for successfully managing your warehouse workforce. We’ve compiled more of them into our playbook.
Strategies to successfully manage your warehouse workforce.
Whether you are overstaffed in your warehouse, you are understaffed or your labour costs are too high. Our new warehouse labour playbook dives into multiple strategies to help you overcome the typical warehouse staffing challenges.
Download your copy to learn more about the most common warehouse labour challenges and how specific strategies and solutions, such as automation, can solve them. It’s available to read below.