Lean manufacturing is an age-old concept, but where did it originate and what does it mean? At Toyota Material Handling UK (TMH UK), we embody the concept of lean manufacturing in everything we do, even creating The Toyota Way — a value-based philosophy that everybody at Toyota lives by.
This blog explores lean manufacturing and what it means to us at Toyota.
What is lean manufacturing?
Lean manufacturing — also known as lean production — is an approach to manufacturing that emphasises productivity and waste reduction.
While organisations adopting Toyota lean manufacturing attempt to streamline processes and increase efficiency, they never do so at the expense of creating more waste, environmental or otherwise.
When you embrace lean manufacturing, you can deliver sustainable value. The path to excellence is made that bit clearer. Customers only pay for what they need and, most importantly, what they value.
Waste in lean manufacturing.
In lean manufacturing, waste is an overarching concept stretching beyond physical excess. Waste is deemed as anything that does not add value in an effort to make software and other products entirely useful for their audience.
Defined as ‘Zero Muda’, which translates to ‘zero waste’, waste can be explained via the Japanese concepts of Muda (uselessness), Muri (unreasonableness) and Mura (unevenness).
In this sense, waste can be anything from the resulting rubbish we most commonly think of and unnecessary activities like transport or processes that involve waiting and/or are prone to error.
The history of lean manufacturing.
Although many individuals and organisations toyed with the fundamental idea of lean manufacturing and put greater emphasis on productivity, Toyota is credited with ultimately progressing and defining this idea into what it is today.
Toyota founder Sakichi Toyoda, his successor Kiichiro Toyoda and chief engineer Taiichi Ohno made strides towards simplifying production processes and, in turn, providing better value. Through a quest for continuous improvement — a philosophy and a pillar of the Toyota Production System known as Kaizen — these three figureheads pioneered lean manufacturing, introducing perfectionism to production.
Internally, this came to be The Toyota Production System, now well-known and studied worldwide.
Today, as the commercial landscape continues to adapt, with the increasing need to be agile to remain competitive, lean manufacturing is more important than ever, proving to be a mainstay in many industries.
Interested in learning the top benefits of lean manufacturing? Click the link below to find out.
What is lean production and what are its advantages?
Toyota lean manufacturing: A philosophy, a framework, a legacy.
Toyota’s concept of lean manufacturing is best explained via The Toyota Way — a definition of our values and way of working. At Toyota Material Handling UK, we do much more than embrace lean manufacturing as a concept. We think of lean manufacturing in everything we do, embodying the term.
A philosophy.
The Toyota Way and its lean manufacturing roots is a philosophy all employees live by. The Toyota Way encompasses all our values, sitting atop our vision of ‘producing happiness for all’ and mission of 'creating mobility for all.’
The Toyota Way is a reference point, helping us realise our Guiding Principles daily.
It is time to embrace the power of lean production.
The first step involves downloading the lean production whitepaper. Learn more about the concept and it can help your business improve efficiency and become more profitable.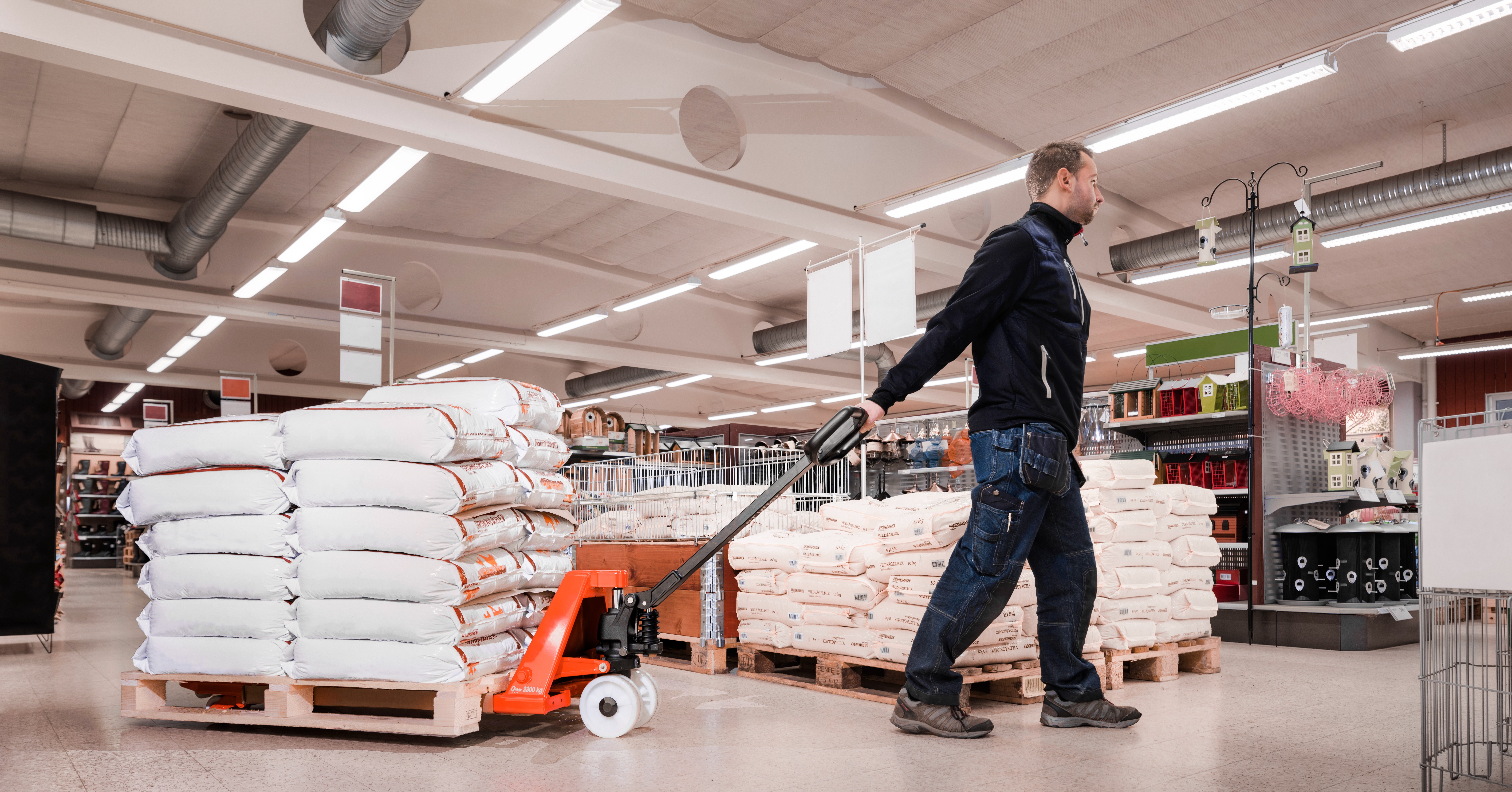
A framework.
The Toyota Way was developed as a framework in 2001 to put Toyota’s values and methods into written form.
As a framework, The Toyota Way is the lifeblood of Toyota. It flows into our corporate culture and extends into all of our work, from software development to our hardware and even the partnerships we form.
Although The Toyota Way was introduced long after our Guiding Principles, it is still connected to these seven truths. The Toyota Way stands alongside The Code of Conduct as a pillar on which Toyota’s Guiding Principles can stand.
The Toyota Way is a framework for applying these principles. It functions to progress software with a people-first design, creating agile hardware that can change with its software and developing partnerships to unite partners, communities, customers and employees.
A legacy.
The Toyota Way and its original concepts are a key part of Toyota’s history. As we follow The Toyota Way, we look to the past and future, remembering the fundamental principles of our production process as it was imagined some 70 years ago.
However, The Toyota Way is not a static concept, stuck in time or frozen in theory. Just like everything else Toyota, it is always evolving to remain effective in an ever-changing world.
When it comes to warehouses, automation is the latest evolution.