Creating and maintaining efficiency is a crucial objective in warehouse management today. Typically, warehouse managers search for ways to improve their processes without completely reinventing the wheel, which is where warehouse layout optimisation becomes invaluable.
Developing clear and efficient pathways throughout a warehouse can eliminate redundant processes, reduce waste and minimise time lost due to unnecessary travel and traffic congestion. Thanks to clearly delineated pathways visible to all, a well-optimised warehouse layout can also lead to fewer accidents or collisions.
While there is no one-size-fits-all approach to warehouse layout optimisation, the following seven best practices will help guide your redesign efforts.
- Mapping your warehouse layout
- Choose your storage areas
- Designate storage space for specific products
- Optimise designs based on your loading and shipping areas
- Prevent bottlenecks in your loading and unloading areas
- Designate reception areas
- Designate areas for picking
1. Mapping your warehouse layout
The first step in warehouse layout optimisation is creating a detailed blueprint of your warehouse. Software like AutoCAD can provide an accurate map to start your redesign. This step includes:
- Taking the most accurate measurements of the warehouse.
- Labelling each area and the direction of the workflow.
- Include common walkways, doors and staircases alongside material flow routes.
- Include space measurements such as length, width and height.
Additionally, calculate your warehouse’s total size in cubic feet. For example, if your warehouse has 25,000 square feet of space and 30 feet in height, it contains 750,000 cubic feet (25,000 x 30). This data is crucial for effective warehouse layout planning. Working with external design experts can further enhance the mapping process and ensure your layout is optimised.
2. Choose your storage areas
The next step in warehouse layout optimisation is determining the size of your storage areas. Calculate the size by multiplying the square footage of your racking by the height of the highest potential load within the storage area. This figure represents your potential storage area size. To find the percentage of your warehouse dedicated to storage, divide this by the total warehouse size and multiply by 100.
For example, if your warehouse storage area takes up 6,000 square feet with a 20-foot height, it offers 120,000 cubic feet of storage. Using the total cubic feet from the earlier example:
(120,000/750,000) x 100 = 16%
A storage area that occupies 16% of your total space is relatively small. An optimised plan typically dedicates around 25-27% of the total space to storage.
This can be achieved by increasing racking or adjusting aisle widths. The ideal storage area size will depend on your production volume and business demand, so consider grouping your storage by product type or setting up storage in aisles. Remember to use vertical space effectively, as it maximises the efficiency of your warehouse layout.
Start your warehouse automation journey, today.
Find out more about warehouse automation, how it works and the benefits it can offer your business by downloading the insightful guide.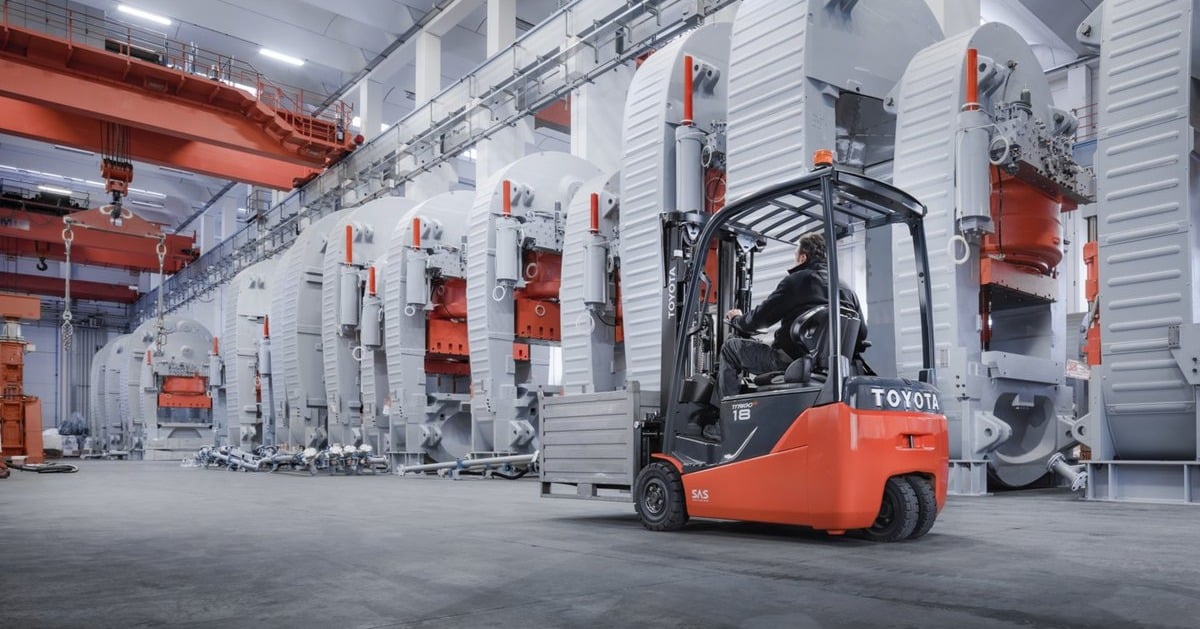
3. Designate storage space for specific products
Storage racks house various goods and materials, and warehouse layout optimisation should maximise the use of these spaces.
For example, think of the space between the top of a stored item and the bottom level of the higher rack. If more than six inches of space is present, you might be underutilising the space. Typically, racks only need about six inches to accommodate forklift interaction.
Additionally, consider whether your racks consistently store the same-sized products. If your inventory varies, designate specific areas for larger and smaller items. This allows the warehouse layout to be optimised by lowering racks to create additional levels above while larger items are stored in designated areas.
4. Optimise designs based on your loading and shipping areas
Warehouse layout optimisation will heavily depend on where the delivery and shipping vehicles are located. For example, here are three potential layouts based on where these lie:
The L-shaped layout
A warehouse may have the loading/unloading space and the shipping space at the tips of the ‘L’. This means the bulk of the workflow — production and storage — should be housed at the ‘L’ intersection.
The U-shaped layout
The U-shaped layout is a standard design. It features production and storage in the bend of the ‘U’ while loading/unloading and shipping occur in the arms.
The I-shaped layout
I-shaped layouts denote a warehouse layout with loading/unloading at one end of the warehouse and shipping at the other. Production and storage are centrally located.
Whichever design you choose, work out where you need to store the high-demand items in relation to your shipping, as these will be the most likely to be bought and shipped. This is known as the dynamic storage area. Less popular items should be stored further away, in the static storage area.
5. Prevent bottlenecks in your loading and unloading areas
To prevent bottlenecks, ensure enough space is available in your loading and unloading areas. This space is crucial for equipment like forklifts or shuttles, as manually moving products is inefficient.
Sometimes, these areas can be separate from the main warehouse, which means that either:
- An automated conveyor system can transport the goods.
- Automated trucks, such as Automated Guided Vehicles (AGVs), can transport goods.
6. Designate reception areas
The reception area is where deliveries are received and where product sorting begins. Again, this needs a lot of space, as too little will create a blockage at the beginning of your warehouse’s workflow.
Accuracy is a must in this area, and goods and materials need to be allocated to the appropriate uses or destinations. Space is crucial, so ensure there is enough space for employees and trucks to enter and exit safely.
7. Designate areas for picking
If your warehouse focuses on shipping, having a designated picking area is essential. This area should be located next to or within storage areas to minimise the time spent searching for items. Implementing machinery such as conveyors and sorters can significantly enhance picking performance. One study found that conveyors increased the pick rate from 60 to 300 per hour.
We have not yet discussed machinery, but it can be a vital part of warehouse layout optimisation, ensuring the workflow of your warehouse is optimised and improved alongside the layout. These things can be achieved in tandem, where you design a new layout based on the machinery you are onboarding.
Automated warehouse logistics, such as AGVs, benefit many businesses and their distribution centres, warehouses and manufacturing facilities. However, you should always determine whether you need them before beginning your research.
In our checklist, we have developed the quickest way to discover if automation is right for you.
The next steps for optimisation
Do you have problems with excess labour or not enough? Is your warehouse experiencing issues with shipping efficiency? Have you experienced on-site accidents with operated trucks in the past?
Our warehouse automation checklist will help you with all the right questions to see if automation will have a significant enough impact versus its investment. Click the link below for your copy and get access to these insights today.