Managing inventory requires a system that increases accuracy and eliminates waste. This kind of system is a vital part of efficient and productive warehouse management. In fact, losing visibility over inventory leads to issues of lost profitability and inaccurate storage and transportation, which negatively impacts your bottom line.
Fortunately, there are many methods you can implement when it comes to improving inventory accuracy. Some require financial investment and others require time and dedication, yet each will accrue net improvements to any warehouse logistics effort. Here are eight ways to improve inventory accuracy.
- Universalise ownership of inventory accuracy.
- Ensure employee training.
- Ensure the right technology is in place.
- Improve your warehouse layout.
- Analyse your current inventory accuracy rates.
- Try lean production.
- Simplify your workflows.
- Tag and track your inventory.
1. Universalise ownership of inventory accuracy.
The accuracy of inventory levels affects the entire profitability of a business. Therefore, ownership and responsibility should be levied against each team member within a warehouse.
While executive management will usually manage inventory with the help of software or tracking systems, it is worth making sure each employee understands the importance of accuracy.
Human error is a big issue for warehouses, with failed deliveries costing money and reputation. Ensure staff are accurately trained in their specific roles and can spot problems in their respective activities. Some may be uniquely positioned to spot inaccuracies before they become an issue.
2. Ensure employee training.
One surefire way of ensuring ownership is through proper and continued training.
Regardless of their position within the warehouse, an employee should be aware of and understand an organisation’s objectives relating to inventory and what inventory management good practice looks like.
Above all, training increases the presence of consistency. In consistency, we find accuracy, where workflows are done in the way they are supposed to be. Highly trained employees can avoid mistakes that other, less experienced individuals may make.
Start your warehouse automation journey, today.
Find out more about warehouse automation, how it works and the benefits it can offer your business by downloading the insightful guide.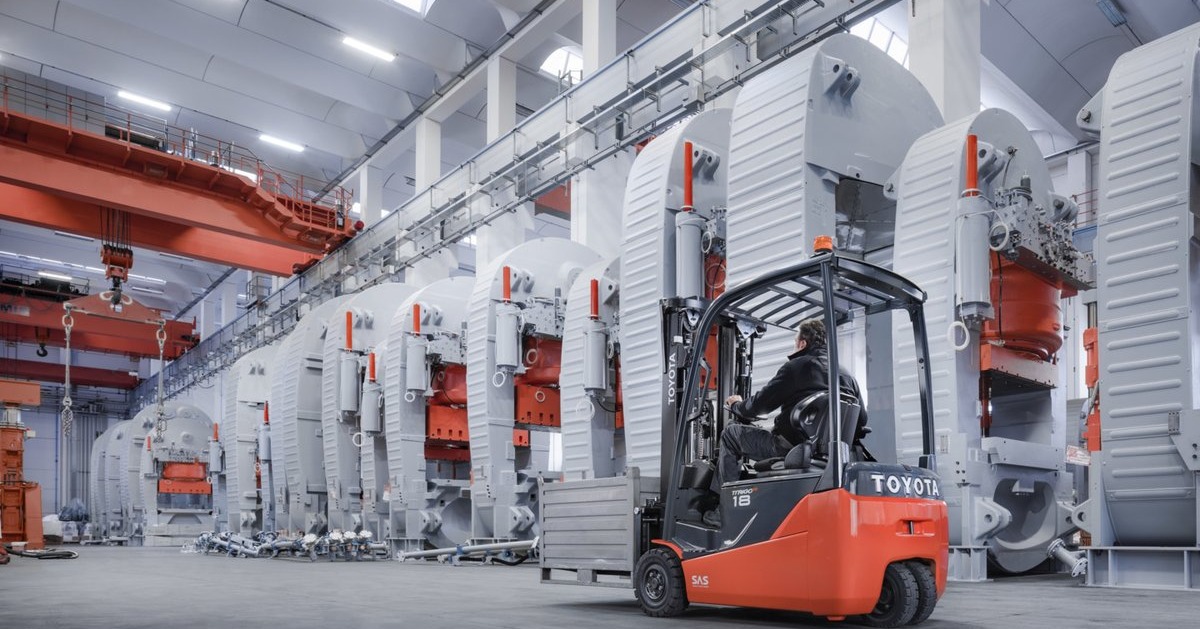
3. Ensure the right technology is in place.
Inventory tracking, asset tagging, warehouse automation — these are all worthwhile investments for the warehouse, improving inventory management accuracy and reduce the potential for downtime-inducing and costly mistakes.
Automation is particularly helpful on the warehouse floor, which enables better tracking of inventory and goods flow as it makes its way through the warehouse. This leads to more efficient manufacturing, delivery and other integral warehouse processes.
You can explore a quick guide to warehouse automation here.
Discover whether automation is right for you.
Automation is quickly becoming an integral part of the modern warehouse. When it comes to inventory accuracy, accident risk and performance, automation is a critical player in improving all of these.
If you would like to discover whether automation would work within your warehouse, download our checklist to warehouse automation by clicking below.
4. Improve your warehouse layout.
A confusing or complex warehouse layout will only upset the efficiency of your workflows. Essentially, every warehouse needs a reliable and optimised layout that covers the flow of material from the point of origin to its final destination.
This means inventory is stored in the correct areas, is more easily accessible and flows better through the warehouse. It is also aided by bringing in automation, such as the solutions offered by dedicated warehouse robotics.
Discover our top tips on improving efficiency and reducing waste through warehouse layout optimisation in this blog.
5. Analyse your current inventory accuracy rates.
What are your current accuracy rates? What percentage of your deliveries are going out on time and without error?
Finding the answer to these questions is vital as it provides a solid, statistical base for further improvement. It provides visibility and an argument for buy-in from management when advocating for a system upgrade or change of operational management.
Your data helps you establish benchmarks, goals, areas to focus on and determine how much you will increase profitability and performance. Without analysing your current position, you are left in the dark. In short, you cannot fix what you cannot see.
6. Try lean production.
Lean production (or lean manufacturing) is where production within a warehouse is optimised to reduce wasted materials. It includes:
- ‘Just-in-time’ manufacturing: This is where material use and inventory are optimised to reside at a level exactly matching the demand.
- Modular thinking: Warehouses are altered to automate repetitive, time-consuming tasks such as handling and transportation.
- Product-wide automation: Automated logistics solutions are brought in to track and maintain the flow of goods through the warehouse, increasing accuracy across the board.
To take a more in-depth look at lean production and its advantages, read our blog post here.
7. Simplify your workflows.
This goes hand-in-hand with optimising the layout of your warehouse. Simplify every workflow on-site by analysing each process and reducing the number of steps involved.
By simplifying your processes, you can even guarantee that employees have more time away from those repetitive, low-value tasks that pile up during the day.
8. Tag and track your inventory.
Every inventory management process will include a way of tagging and tracking both inventory and assets. This means utilising barcode scanners and SKUs to adequately label inventory and keep people notified about where it resides in storage areas.
Being able to trace products accurately is the be-all and end-all of inventory accuracy. It means you have full visibility and requires that inventory never be moved without authorisation.
Find out more about improving your warehouse's internal processes.
These eight steps will enable any warehouse to track its inventory more accurately. But if you need more, our blog is home to unique insights on how you can improve the internal processes of warehouses, manufacturing facilities and distribution centres — and much more.
To gain access to these regular insights, click the button below.