Lean production is a series of methods designed to minimise the waste of material and labour while maintaining or increasing levels of production within a warehouse.
When implemented effectively, lean production can offer many benefits, including increased profits, improved lead times and a more sustainable business model.
There are several lean production techniques your business could implement. This blog will outline some of the most popular methods and why they are so effective. These include:
1. Kaizen.
The Kaizen methodology is a strategy that focuses on continuous improvement. It aims to gain buy-in from everyone to work together and proactively achieve regular, incremental improvements to the manufacturing process.
The ultimate goal of Kaizen is to ensure maximum quality, fast track waste elimination and improve efficiencies, both in terms of equipment and work procedures. Kaizen also aims to humanise the workplace by empowering individual members to identify areas for improvement and suggest practical solutions.
In turn, this also improves employee morale. As employees see their ideas and suggestions are taken seriously and implemented in a warehouse, their enthusiasm can increase significantly.
Find out more about Kaizen and how you can implement this methodology into your business strategy by downloading our insightful guide.
2. The 5S methodology.
The 5S methodology is a systematic approach to workplace organisation. This method includes the five steps of sort, set in order, shine, standardise and sustain.
These steps involve going through everything in a warehouse and deciding what is necessary and what is not. This includes everything from processes and technology to materials and tools. This methodology is often considered the foundation of lean manufacturing because, for a workplace to reduce waste and become more efficient, it needs to be organised first.
In addition to reducing waste, the 5S methodology can provide many benefits to a warehouse, including improved maintenance and safety, better efficiency across your operation and more committed employees.
Is your business ready to harness the power of lean production?
If so, download this guide. You will learn about the benefits of lean production and discover the most effective techniques to implement to achieve success.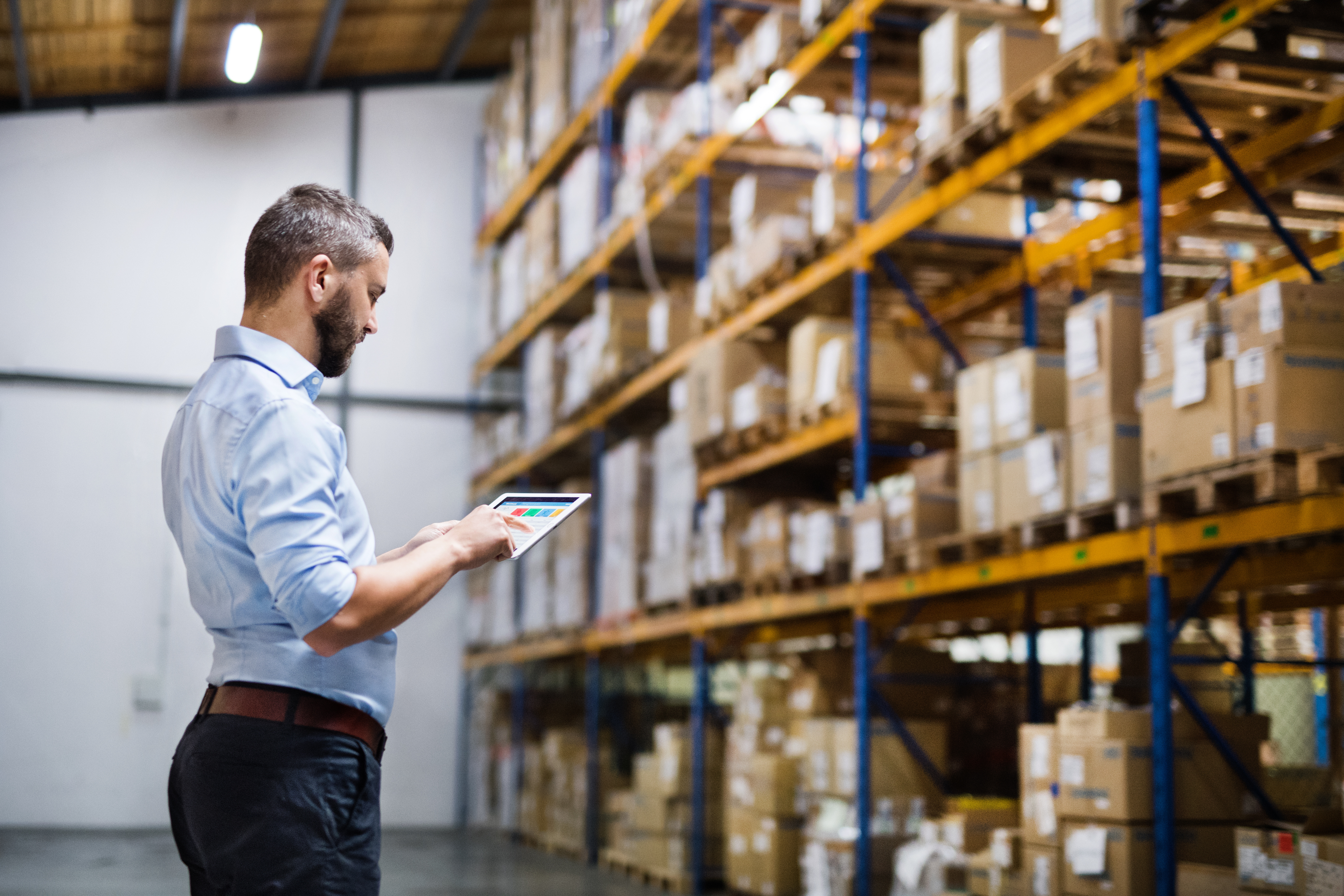
3. Value stream mapping (VSM).
VSM is a lean management tool that allows businesses to visualise the steps needed to create optimum value throughout the supply chain. By reviewing the flow of process steps and information from origin to delivery, companies can quickly detect waste areas and mitigate them.
VSM also provides warehouses with a single source of truth. This enables them to improve their decision making, facilitate clear communication across different departments and ensure quality is maintained across every stage of a product life cycle.
You can discover more about VSM and why it is deemed one of the bedrocks of lean production by downloading our guide.
4. The six big losses.
The six big losses is another lean tool used in warehousing to establish the most common waste areas in an operation and make relevant changes to reduce them. These losses can be broken into three categories: availability, performance and quality.
Availability losses include a range of potential wastages such as machine failures, the unexpected breakdown of equipment and material shortages. Performance losses are related to small stops and reduced speed due to poorly maintained or slow equipment, substandard materials that damage the equipment or inexperienced operators running the equipment.
Quality losses involve process defects and reduced yield. Process defects are commonly caused by incorrect equipment settings, operator errors and poor equipment handling.
Reduced yield accounts for the defective parts produced in the warm-up stage of production. It is caused by poorly executed changeovers, wrong settings or equipment generating waste after startup.
5. Bottleneck analysis.
Bottlenecks in an operation result in lost time, one of the most common causes of waste in the warehouse industry. Therefore, businesses should identify the cause of a bottleneck and find a way of eliminating it from occurring again in the future.
This can be done through bottleneck analysis. Once the cause of the bottleneck is identified, the company can work towards potential solutions to push products through the production line at a more consistent rate again.
As well as improving workflows, bottleneck analysis can also eliminate waste and increase knowledge. The more a business knows about a process, the easier it is to make better decisions moving forward.
Our guidance on lean production does not end here.
All of the methods mentioned above are key aspects of embracing lean production. However, there is so much more to know about and we have covered everything in our new guide.
Learn more about the benefits of lean production, the eight wastes of lean production and the role technology plays by downloading your copy.