According to HSE reporting, 36.8 million working days were lost between 2021 and 2022 due to work-related illnesses or workplace accidents, with an estimated cost of £16.2 billion.
For businesses operating warehouses, distribution centres or manufacturing facilities, avoiding downtime is vital to maintaining performance and profitability. To reduce the risk of warehouse accidents, companies should be aware of the following:
- The most common causes of warehouse accidents.
- Examples of warehouse accidents.
- How to reduce the occurrence of warehouse accidents.
- Is warehouse automation right for your business?
The most common causes of warehouse accidents
Warehouse accidents can happen for several reasons. Sometimes, they occur due to a specific circumstance, such as a slip caused by a wet floor, but they're often due to a lack of planning and preparation.
Luckily, many accidents can be prevented through proper awareness and preventative measures.
Lack of signage
Warehouses require safety signs to designate hazardous areas due to dangerous machinery or high traffic. Without warning signs, warehouse accidents are likely to occur.
Irregular equipment maintenance
All warehouse equipment needs maintenance. It is likely to cause an incident when it is in poor condition.
When purchasing warehouse equipment, ensure the provider can deliver direct maintenance from in-house engineers or recommend a third party to maintain the equipment.
The type of equipment purchased is also worth consideration, as automated and electric vehicles often require less maintenance and pose less risk towards workers than combustion engine vehicles.
Improper training
Without the right training, employees may use unsafe working methods that risk injury. Employees must receive proper training to reduce warehouse accidents. The risks of improper training are compounded by poorly maintained machinery and can lead to workplace accidents of varying severity.
Poorly designed warehouse layout
Another critical yet much-overlooked cause of warehouse accidents is a poorly planned warehouse layout.
Buying or renting a warehouse and filling it with equipment or storage is simple, but warehouses must be set up more efficiently. In the perfect scenario, the flow of goods is tracked and unimpeded by poor layout.
Optimised warehouses utilise modular thinking, where common functions can be adapted as configurable modules for repetitive usage. This is an excellent opportunity to introduce automation to the warehouse, which helps reduce accidents by optimising the flow and route of goods.
When a warehouse layout and supply flow are optimised, management and workers have more visibility over where goods are going and coming from, dramatically reducing the potential for accidents caused by traffic or improperly stored materials or products.
For example, common causes of injury happen through forklift and pallet truck misuse, whether through staff being struck by these machines or because trucks are in poor condition. According to the British Safety Council, 1,300 employees are injured yearly because of improper truck use.
Optimising a warehouse includes improving the usage of these kinds of machinery, which require proper delineation of gangways for effective use.
Start your warehouse automation journey today
Find out more about warehouse automation, how it works and the benefits it can offer your business by downloading the insightful guide.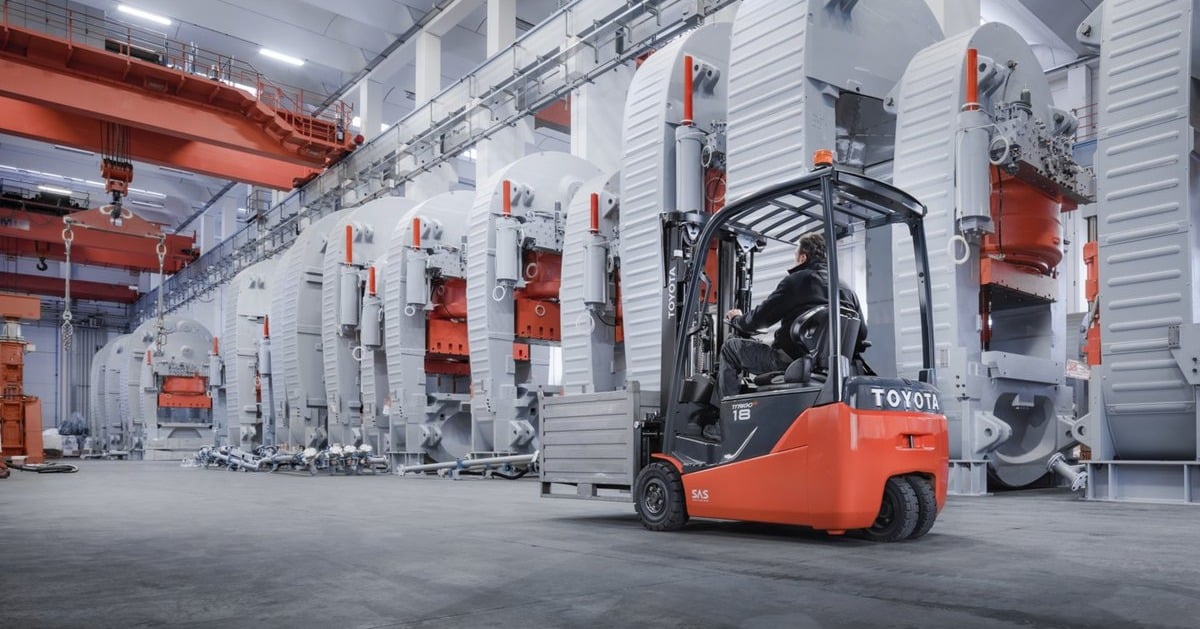
Examples of warehouse accidents
Slips, trips and falls
Some of the most common examples of warehouse accidents are slips, trips and falls, which account for 29% of non-fatal injuries. Uneven or slippery surfaces, or unseen hazards such as discarded material can cause these.
Manual handling
Handling, lifting or carrying caused 18% of non-fatal injuries. In warehouses, many raw materials are large, heavy loads. Repetitive lifting can be strenuous in areas such as the back or knees. Similarly, a lack of training will see employees lifting heavy objects unsafely, resulting in anything from minor sprains to chronic conditions and musculoskeletal disorders.
These injuries significantly impact the affected parties' lives, resulting in downtime and potentially impacting productivity. So, how can businesses reduce the risk of warehouse accidents?
How to reduce the occurrence of warehouse accidents
Primarily, businesses can protect employees by investing in suitable training for handling goods and using machinery. These are preventive measures, immediately targeting those with the potential of harm.
Warehouse automation
However, while training minimises risk, a surefire way of decreasing warehouse accidents is by eliminating waste and hazards within the warehouse. A proven method to achieve this is by optimising the warehouse with automation.
Automation requires using Automated Guided Vehicles (AGVs) that are programmed to work autonomously, maintaining the flow and visibility of goods throughout the warehouse. They need no driver or operator, working from pre-programmed pathways developed to ensure the most efficient use of space.
As the AGVs stick to delineated pathways and take over the manual handling of goods that employees traditionally undertook, the risk to employees is significantly reduced.
For example, automated solutions:
- Reduce the 18% of injuries caused by manual lifting and handling. Automated trucks take over these duties.
- Reduce the 11% of injuries caused by being struck by a moving object. Automated solutions such as AGVs operate within delineated boundaries and utilise scanners that detect obstacles, stopping them before impact.
An excellent example of automation in practice is a goods-to-man picking solution. This involves automating the movement of goods by utilising technology such as automated shuttles and conveyor systems.
Goods are rapidly transported to ergonomic picking stations where workers can collect the items needed for an order or product. It eliminates the need for human operators to search for items or move them manually, reducing the likelihood of workplace accidents.
Is warehouse automation right for your business?
Automation offers flexibility, visibility and a proactive warehouse and supply chain management approach. It works exceptionally well within specific scenarios and helps minimise the occurrence of workplace accidents, helping to boost overall performance.
Inside this checklist, discover whether your scenario could benefit from automation. Click the link below to download your copy and gain access to the insights today.