Lean production can offer many benefits for supermarket warehouses. Not only is it an effective way to improve performance, but it can also support a business in building a sustainable operation.
By using different lean tools and techniques, a company can identify issues within its operation. Warehouses can then implement innovative tools such as warehouse automation to make improvements quickly.
This article will discuss some of the lean tools and techniques a supermarket could consider implementing, alongside the role technology can play in the process.
- Kaizen.
- The 7 wastes of lean manufacturing.
- Value stream mapping (VSM).
- The 6 big losses.
- Bottleneck losses.
Kaizen.
The Kaizen methodology focuses on continuously improving operations and involving all employees throughout the process.
Instead of hoping for a business to improve overnight, Kaizen expects the process to be gradual, with regular tweaks and changes happening to an operation along the way.
For a supermarket warehouse, two of the key objectives are to ensure stores keep their shelves fully stocked at all times and meet online order demands.
Of course, this can be difficult. Using the Kaizen methodology, a supermarket can pinpoint periods where they struggle to meet demand and implement new solutions such as warehouse automation to overcome challenges.
The 7 wastes of lean manufacturing.
The 7 wastes of lean manufacturing focus on removing waste from an operation. For most supermarket warehouses, the waste production is a big issue.
There are three main types of waste in supermarket warehouses. These include:
- Energy consumption waste: This includes the unnecessary use of energy in a warehouse, including transportation costs and the overuse of electricity.
- Resource consumption waste: Labour costs can quickly add up in a supermarket warehouse. Fluctuating demand can make it difficult to forecast labour.
- Packaging and material consumption waste: When a certain product does not make it to the shelves, it gets thrown away, also resulting in unnecessary waste in the warehouse.
By using the 7 wastes concept, supermarket warehouses can establish the types of waste they are producing and implement solutions such as Automated Guided Vehicles (AGVs) to remove them.
Is your business ready to harness the power of lean production?
If so, download this guide. You will learn about the benefits of lean production and discover the most effective techniques to implement to achieve success.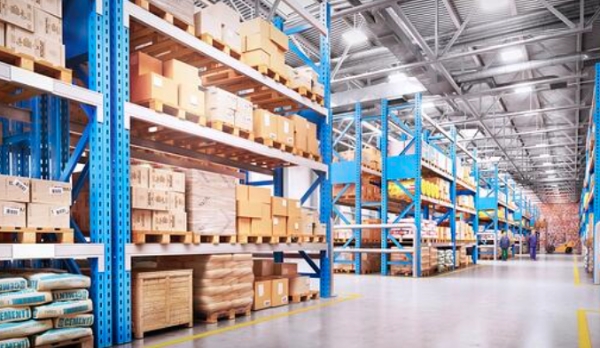
Value stream mapping (VSM).
VSM is a lean management tool that provides businesses with a clear visualisation of the steps they need to take to create optimum value in their supply chain. This is done by visualising the flow of every single product from the warehouse to the customer to identify delays and processes that do not add value.
When flow is ‘good’, work moves steadily and predictably concerning customer demand and supplier capacity. When flow is ‘bad’, work is erratic, resulting in frequent interruptions and lost productivity.
A supermarket warehouse can use this tool to better manage inventory, improve lead times in the production cycle and identify delays. Once these delays have been identified, the next step involves implementing automated solutions that can remove these delays, such as a Warehouse Management System (WMS).
The 6 big losses.
The six big losses is another lean tool used in supermarket warehousing to establish the most common waste areas in an operation and make relevant changes to reduce them. These losses can be broken into three categories: availability, performance and quality.
Availability losses in a supermarket warehouse might include machine failures or material shortages such as food and drink packaging. Performance losses are related to small stops and reduced speed due to poorly maintained or slow equipment, while quality losses involve process defects and reduced yield.
Once these losses have been identified, a supermarket warehouse should implement machine learning algorithms and robotics solutions that can effectively reduce the types of waste mentioned above.
Bottleneck analysis.
Bottlenecks can happen quite regularly in a supermarket warehouse. These types of bottlenecks can vary from staffing issues to machinery breaking down.
These situations should be avoided, resulting in lost time and profitability. To make this happen, a business should undertake a bottleneck analysis regularly.
Once you have used the bottleneck analysis to identify areas for improvement, your warehouse can implement solutions such as collaborative mobile robots, automated storage systems and other types of automation to avoid these bottlenecks happening again in the future.
Ready to start harnessing the power of lean production at your business?
Lean production can offer many benefits to supermarket warehouses. There is no doubt about it. As well as being a productive way to streamline and improve production systems, it can support you on your sustainability journey.
However, before you leap, you should weigh up the pros and cons of the concept and clearly understand the different strategies available.
We want to help you do that. That is why we have created an in-depth guide that covers the tools and techniques above in more detail and addresses the benefits of lean production.
It is time to get started. Download a copy of the guide below.