In lean manufacturing, waste can be defined as anything that does not add value to the production process. To help businesses establish their different types of waste, they can use the concept known as the ‘7 wastes of lean manufacturing’.
The concept dates back to the middle of the 20th century and is a core principle of the Toyota Production System (TPS). This article will explore the seven wastes of lean manufacturing in detail.
Transport.
Transportation waste includes the movement of people, tools, inventory, equipment or products. The excessive movement of these types of waste can lead to damage and defects.
Therefore, warehouses should implement initiatives to limit their transportation waste. An example of this includes optimising the layout of a warehouse.
This involves developing clear and efficient paths, optimising storage areas and preventing bottlenecks in loading and unloading areas.
The type of equipment you have on-site can also contribute to the optimisation of your warehouse’s layout. Solutions such as Automated Guided Vehicles (AGVs) can work autonomously, transporting goods and materials through manufacturing facilities.
As they are automated, they are far less fallible than human workers. Reducing human error is a crucial way of improving efficiency and accuracy on the warehouse floor, helping minimise loss and downtime, alongside capturing improved resource utilisation. Additionally, these vehicles are battery-powered, meaning that they produce zero emissions and are far kinder to the environment.
Inventory.
Having more inventory than necessary can lead to a combination of waste building up. These include:
- Product defects.
- Damaged materials.
- Longer lead times across the production process.
- An inefficient allocation of resources and capital.
Several strategies have been designed to support businesses to prevent inventory waste. Having a contingency plan in place for when equipment fails is crucial.
As well as this, your business should implement an inventory management system if you do not have one already.
A good inventory management system will help your business keep quality levels high, reduce inventory shrinkage and ultimately reduce excessive inventory waste.
Motion.
The waste in motion includes any unnecessary movement of people, equipment or machinery. Any tasks that require excessive motion should be redesigned to enhance workplace performance.
This can be done by ensuring your warehouse is appropriately organised and putting materials in an ergonomic position to reduce stretching and straining.
Over excessive motion can lead to increased warehouse accidents and injuries. The estimated cost of injuries and ill health from working conditions was £16.2 billion between 2019 and 2020.
Another critical yet much-overlooked cause of warehouse accidents is a poorly planned warehouse layout. Be sure to design a warehouse that takes motion waste into consideration, too.
Is your business ready to harness the power of lean production?
If so, download this guide. You will learn about the benefits of lean production and discover the most effective techniques to implement to achieve success.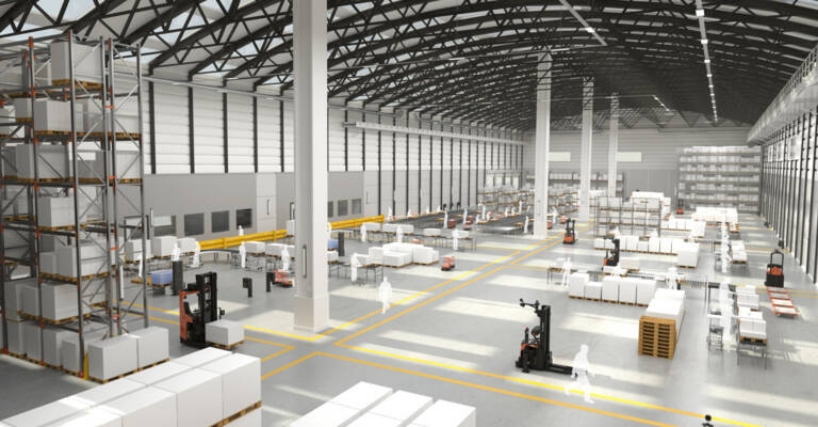
Waiting.
When the production line stands still, time does too. Your staff can not complete their jobs, resulting in excessive waste building up in your warehouse.
Some of the main reasons waste can become an issue in a warehouse include unplanned downtime, a lack of processes in place and lack of communication.
The steps your business can take to eliminate waiting waste involve redesigning processes related to production flow and standardising instructions and training across departments.
Overproduction.
When a warehouse overproduces the levels of inventory needed to meet demand, this is known as overproduction waste.
Overproduction often leads to the waste of resources and time. Any amount of time or resources used to produce a product beyond the customer’s requirements is considered waste.
One of the most effective ways to avoid overproduction in your warehouse is by introducing labour forecasting. This can be done by investing in the right technology to harness the power of data and predict the optimal labour requirement needed during fluctuating periods of demand.
Overprocessing.
Every warehouse needs processes in place. However, excess processing can harm the entire production chain.
Examples of excess processing include running more analysis than required to meet specifications, having to adjust components after installation or over-engineering products, all of which will unnecessarily increase your costs, time and resources.
There are many initiatives your business can incorporate to reduce overprocessing waste. The first and most crucial step is to have a clear schedule and work plan that your entire workforce is engaged with.
The 5S methodology can also help you improve your business processes. This involves going through everything in a warehouse and deciding what is necessary and what is not. You can learn more about the methodology here.
Defects.
Defect waste occurs when a product is found to have flaws once it has made its way through the production process.
Of course, a product with flaws cannot be sent to the customer, meaning it usually gets thrown away. This results in resources being wasted, including time and money.
Automated warehouse solutions are one of the most effective ways to eliminate defects. With modern, integrated and intelligent software, human inaccuracies regarding inventory control and management can be quickly removed.
Ready to learn more about lean manufacturing and how it can be implemented in your business?
We have created a guide that focuses on harnessing the power of lean production. The guide covers various topics, including the benefits of lean production and the techniques you can deploy in your business.
It is time to get started. Download your copy below.