Inefficient processes in warehouses can lead to bottlenecks in the supply chain, miscommunication between teams and increased staff turnover. Ultimately, these types of issues can have a detrimental impact on a warehouse’s operation. So, what can you do to optimise them?
Thankfully, there are a range of solutions available. However, for your business to reap the benefits, you need to adopt a lean way of thinking, where continuous improvement becomes the bedrock of everything you do. This article discusses some of the solutions your business can embrace to reduce inefficient processes and continually improve your warehouse operations.
- Adopt the right technology.
- Optimise the layout of your warehouse.
- Focus on increasing labour efficiency.
- Implement lean production techniques.
1. Adopt the right technology.
For businesses struggling with inefficient processes, technology such as automation can take many of your troubles away. One of the key benefits is that automated solutions can complete many of the manual tasks a person would usually take on.
A recent study found that 693,000 non-fatal injuries were caused by handling, lifting or carrying out tasks in the warehouse in 2020. Workplace injuries are one of the most common disruptors to warehouse processes each year. They cause delays, unsettle the workforce and harm the bottom line.
As well as being an effective way to reduce workplace injuries, warehouse automation can also support your business within other aspects of your operation. These include improved inventory accuracy, the minimisation of warehouse errors and increased workplace morale.
Sustainability is another advantage of using warehouse automation, as AVGs (automated guided vehicles) run primarily off lithium-ion batteries which are much more environmentally friendly than their combustion forklift counterparts.
In addition to automation, there are other technological solutions your warehouse could look to implement such as the I_Site fleet management tool powered by Toyota Material Handling.
This solution is designed to use data from your smart trucks to measure, analyse and maximise the performance of each connected machine.
This gives you the ability to take control of your entire truck fleet to strengthen your long-term business profitability and make better decisions as you move forward.
2. Optimise the layout of your warehouse.
The layout of your warehouse is crucial for improving processes. This is because an optimised warehouse layout prevents bottlenecks, makes it easier for staff to complete their job and stops accidents from occurring.
Making changes to your warehouse layout may seem like a big change. People will have to get used to a new working environment and they may likely face some challenges along the way.
However, it is essential to remember that you do not have to get it right the first time. There are different types of layouts you could implement and it might take some trial and error before you establish which one is the best fit for you.
To get a clear picture of the best warehouse layout for your business, be sure to regularly ask for feedback from your staff. Ultimately, they are the ones who can decide if it has made a difference.
Once you have gathered feedback, you may want to consider a service such as LSI. Here, our team of specialists will analyse your entire operation and make recommendations to optimise your warehouse layout and ensure you have the most suitable solutions across each area of the supply chain.
Is your business ready to harness the power of lean production?
If so, download this guide. You will learn about the benefits of lean production and discover the most effective techniques to implement to achieve success.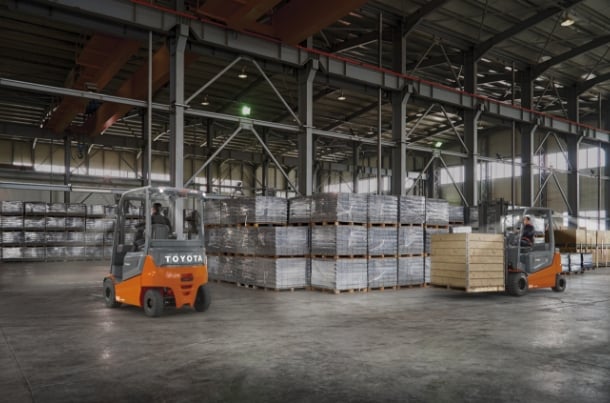
3. Focus on increasing labour efficiency.
Fluctuating demands are destined to take place in a warehouse. You are likely to face busier periods and quieter ones too. What is important is ensuring you have the correct number of staff working during these fluctuating periods.
This can be done through labour forecasting — the process of anticipating how many hours a business will need its employees to work in the future to meet demand.
Technology can support you on your mission. A warehouse management system (WMS) can provide you with visibility of your inventory and supply chain fulfilment to predict future labour trends.
From here, you can make continuous improvements to ensure you meet demand and staff work in the most efficient way.
4. Implement lean production techniques.
The lean methodology was built on the Japanese term, Kaizen. This term means “continuous improvement” and sees improvements in the warehouse as a gradual and methodical process. Your business can implement several lean techniques to begin removing inefficient processes and continually improve your entire production chain. These techniques include:
The 5S methodology.
This process is focused on going through everything in a warehouse and deciding what is necessary and what is not. From here, you can pinpoint redundant processes and make better decisions on the type of solutions needed to remove them.
The 5S methodology is also key for warehouses looking to reduce waste, improve maintenance and increase employee engagement.
The six big losses.
The six big losses is another lean tool used in warehousing to establish the most common inefficient processes in an operation and make relevant changes to reduce them. These losses can be broken into three categories: availability, performance and quality.
For example, you may have machinery in your warehouse that regularly breaks down and disrupts operations. If so, the six big losses will help you determine the true impact this is having and implement solutions to replace the machinery.
Bottleneck analysis.
Bottlenecks usually take place because a process is not working effectively. By undertaking analysis, you can determine the root cause of the bottleneck and eliminate it from occurring again in the future.
The more knowledge you have about your bottlenecks and why they are happening, the quicker you can implement solutions aimed at reducing them.
These are just a few examples of lean techniques your business could implement to improve your warehouse processes. There are many more and we have put together a guide that delves into some of them.
Download your copy of the guide to learn more about the benefits of lean production, the most effective techniques and how your business can start to adopt a lean way of thinking.
Access your copy below.